Need more details?
What is the most suitable system for my company?
From an economic and manufacturing point of view, choosing the right pneumatic conveying system is not easy for everyone. Let’s start saying that there is no standard that determines with absolute certainty whether a pneumatic system operates in dense or dilute phase. Just because a system has a rotary valve does not necessarily mean that it is operating in dilute phase, just because it has a propeller (the transporter) does not necessarily mean that it is operating in dense phase. To try to make this distinction, however, a few pointers may be useful:
- Many pressure-diluted systems operate at less than 1 bar, typically between 0.2 and 0.6 bar, while dense-phase systems operate at more than 1 bar.
many suction diluted phase systems operate at less than 0.4 bar, typically between 0.3 and 0.4 bar, while dense phase systems operate at more than 0.4 bar, typically between 0.4 and 0.5 bar.
although related to the material to convey, many dilute phase systems, both pressurised and suction, operate at air speeds between 65 and 170 km/h, while dense phase systems, both pressurised and suction, operate at less than 55 km/h.
in dilute phase pneumatic conveying systems, the speed of the material being transported is very close to that of the air in the pipes, whereas in dense phase systems, the speed of the material is much lower than that of the air.
Main factors to consider
When deciding whether to adopt a dense or dilute phase pneumatic conveying system, the first thing to consider is the nature of the material to be moved. Main characteristics in this respect are: particle size and shape, apparent density, moisture content, abrasiveness and friability level. Secondly, cohesion, hygroscopicity (the ability to absorb water molecules), static charge, explosiveness, toxicity and melting point.
Then, it is necessary to consider how and where the system has to be installed. How will pipes and systems have to fit into your warehouse or company premises? Are there volumetric constraints, such as other machinery or low ceilings? The changes to be made to the system in order to adapt it to these constraints must be examined, as well as ensuring the right spaces for any future maintenance.
The last factor to take into account is the amount of material you want to transfer per hour.
Choosing the right pneumatic conveying system
In the preliminary phase, technicians will assess the feasibility of the system. If the material to be moved is not extremely sticky, does not have a very high bulk density and is made up of compliant elements, it can be moved. Then, in order to understand which type of system to adopt, we start with a cost analysis. The initial investment to implement a dilute phase system is lower than for a dense phase system. However, also considering the long-term running costs, it requires larger pipes and filters, is more prone to deterioration and the star valve requires recurrent maintenance.
Suction, pressure, dense or dilute?
We then move on to consider the operation mode. Whether the dilute phase system should operate under suction or pressure depends essentially on two factors: air losses and the material behaviour during transport. If air losses into and out of the system will have negative effects, such as with toxic or explosive materials, a suction system will be the best choice. A suction pneumatic conveying system is also the best choice when the material tends to compact tightly during handling, as wood chips do. Suction is also the choice if the substance is extremely cohesive and prone to accumulate on surfaces, such as titanium dioxide, or if it is very fibrous, such as buckwheat hulls. This is why suction tends to keep the material particles separated during transport, whereas pressurised systems compact them together and on the pipe walls.
On the other side let’s see when the dense phase may be the best solution. Dense phase systems rely on high flow velocities to keep the material entrained by the air stream. On the contrary, high velocities can damage friable materials, resulting in increased friction and product waste. Another undesirable consequence can be the separation of mixed materials during transport. This occurs especially when the mix is made from substances with very different particle sizes and varying apparent densities. The third problem with the dilute phase is that combining abrasive materials with high speeds, the conveying lines and other components wear out more quickly. In all three cases, the smoother transfer provided by the dense phase, which relies on high pressure differentials rather than high speeds, is often a better option.
How piping influences
A further factor in the choice is the length of the transport lines required by the system. The dense phase generally needs smaller diameter piping than a dilute phase system of comparable size. This means that dense phase systems not only require a smaller volume of air, but also require less heavy piping, making them easier to install and replace.
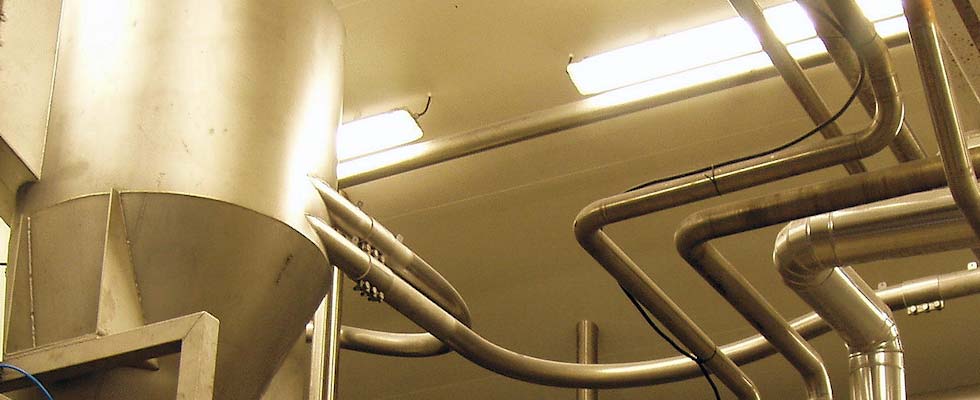
Utility of pilot plant tests
In some cases, when choosing a pneumatic conveying system, real simulations may be necessary in order to have more data to support it. Once it has been decided whether the system will be in dilute or dense phase and whether it will operate under suction or pressure, a series of tests with a pilot plant should be carried out before its construction. This can be a post design step if you are working on a particularly complex, large system under extreme conditions.
The tests will obviously have to be carried out with the same material that will be used to handle the final plant and will have to simulate field conditions as much as possible. The pilot plant must have the same length of the transport lines, the same route and the same number of curves. The tests should be conducted under the same temperature and humidity conditions as at your company site. Before the tests are carried out, the relevant parameters are defined, such as the used air volume, the hourly flow of material and the maximum permitted friction. The tests results on the pilot plant are used to size more accurately the final system and to better understand possible problems in the long and very long term.