Need more information?
Big bag reconditioners for sale
In the industrial world, big bags are large container bags, generally made of polypropylene raffia, equipped with handles and designed to hold hundreds or even thousands of kilos of material. They are used to handle raw materials such as food flours, polymers, plastic powders, but also fertilisers, resins, sludge and even more compact materials such as aggregates and bricks. Widely used and important, they allow to purchase very large quantities of product, with consequent consistent reduction of price.
Because of their size, when they come from far away, they almost always travel in containers by ship. For some substances, such as paint additives or sugar, the long months of transport can lead to the big bags becoming compacted. The material inside them thickens and becomes so cohesive that it forms a single monolithic block very difficult to handle and, in fact, prevents the product from being extracted. This phenomenon depends primarily on the absorbed moisture and temperature changes, so not only transport, but also inappropriate storage can trigger the problem.
If you find yourself in the position of having to disintegrate these bags to be able to use their contents in a fluid way and you don’t know how to do it, you are in the right place. Apply developed a big bag reconditioner, an industrial machine that massages the bags in depth on the four sides and throughout their height. This means that your big bag can be emptied as easily as the day it was filled.
A widespread problem
Working for many years in the world of pneumatic conveying, we had the opportunity to experience the most common situations that companies are likely to improve with our systems. At the same time, we also come into contact with problems that, although not strictly related to pneumatic transport, are recurrent among our customers. One of these is the classic “hardening” of big bags, those huge bags weighing hundreds of kilos that are bought to supply raw materials for production and which, for our pneumatic conveying systems, are one of the sources of material to be handled. We thought it might be useful to do something to make these big bags reusable, so that we don’t have to throw away material and thus save money. Based on our experience, we developed a big bag reconditioner, which has been designed also considering needs from companies that had the same problem in the past.
How the big bag massager works
All the work is done by two crushing plates, each horizontally driven by a pair of pneumatically controlled hydraulic pistons. If the plates are the hands, the heart of the machine is a hydraulic pump, source of force for even the toughest and most difficult big bags. Then there is the brain of the system, the PLC controller, that defines and memorizes the massage sequence in all its variations (piston stroke, frequency, position, speed, side and height), without ever breaking the bag. Finally, the legs, the pallet wheel that enables the massage action on all four sides. The system is anchored to its skeleton, a self-supporting rigid closed frame, within which all the reactions to the high stresses are discharged. The reconditioner is also equipped with protection against the risk of the operator being crushed by means of light barriers.
One of the advantages of the reconditioner is that it takes up very little space, both in terms of floor space and height. This, together with the fact that the big bag can be loaded onto the pallet wheel using either a forklift truck or a pallet truck, means that the installation can also be carried out in cramped and elevated areas. The reconditioning cycles, known as recipes, can be carried out either manually or automatically and are programmable and memoizable via touch panel. Defining, saving and recalling the massage recipes, depending on the bag to be treated, means a considerable reduction in downtime and the possibility of reconditioning even big bags that are almost completely full.
Oversized hydraulic pump
Automation achieved thanks to the Siemens S7-1200 PLC
Frame verified with finite element method (FEM analysis)
Painted carbon steel execution
4 safety light curtains monitored by control unit, protection degree SIL 2 (EN 62061) cat. 3 PLd (EN ISO 13849-1)
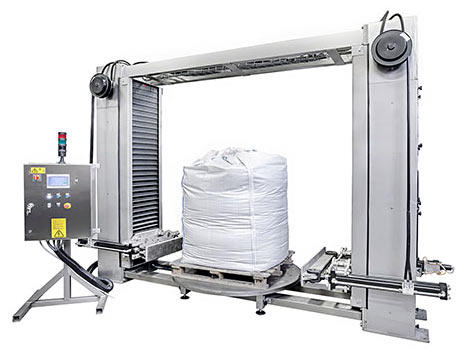
Additional features and accessories
On request, the big bag reconditioner can be adapted to specific requirements and comes with various accessories, see in detail.
It can be modified for ATEX hazardous environments. The small number of electrical components allows the costs of this modification to be reduced compared to competing equipment.
AISI 304 and AISI 316 stainless steel executions.
Equipped with a closing system consisting of 3 fixed gates, one of whom can be opened with a safety microswitch.
If you are not equipped with a pneumatic network, we supply a compressed air kit consisting of a 7.5 kW screw air compressor with low energy impact.
For all types of big bags
Our reconditioner is suitable for all types of big bags. Although practically all of them are made of polypropylene parts, these bags are produced in different ways depending on their use. In terms of size, the standard size is 90×90 centimeters, while the most common heights are 120 and 160 centimeters. In terms of construction method, we can divide them into two main categories: the U-panel model and the tubular model. The U-panels have a U-shaped body to which two panels are joined with vertical seams; there is also a version with four equal size panels sewn together. In both cases, there are four slots at the top for lifting purposes. The tubular model, on the other hand, still has four eyelets, but has no vertical stitching as it is made of circular fabric. It is therefore designed to carry fine products such as powders or granules, because it provides better protection against moisture and reduces the possibility of spillage.
Other differences can be found in the upper part, which can be open, closed with a loading valve for powdery products, or with a candy closure, i.e. tying the four flaps together. Similarly, the lower part can be flat-bottomed, closed with a discharge valve or fully open. Finally, there are a number of treatments that can be applied, starting with UV protection against sunlight. It is also possible to laminate the inside of the bag with polyethylene foil using a hot process to make the bag more stable, to prevent moisture build-up and to prevent dust from entering. Whatever your big bag type and size, the Apply reconditioner can treat it and make it quickly reusable.