Do you need to transport products in your company?
Pneumatic conveying is a functional and effective way of moving powdery, floury and granular materials and, more generally, all materials that can be fluidised within a production site.
The most commonly handled products with this technology include cereals, flour, semolina, sugar, cocoa and bran. Non-food products include cement, wood chips, sawdust, sand, plastics, ash, chemicals, coal and salts. Transport takes place inside closed pipes, thanks to the thrust and fluidifying action exerted by a high speed gas, usually air, on the material to be moved.
The structure of a pneumatic conveying system can be composed by 5 macro blocks. The main one is undoubtedly the electrical machine that moves the air in the system, which may be a blower, a compressor, a pump, a vacuum unit, etc. This is followed by a section designed to dose the material to be transported into the next block, which is the set of pipes connecting the supply point to the discharge point. It will then be necessary to have a device to separate the material from the conveying air and finally a block for expelling the air, possibly accompanied by filtering.
Pneumatic conveying under pressure and vacuum
The mentioned five functional blocks are present in all pneumatic conveying systems, even when they are categorised according to the operation method. Two main categories can be distinguished: pneumatic vacuum conveying systems and pneumatic pressure conveying systems. In vacuum conveying systems, also known as “suction” systems, movement is carried out through a vacuum created in the line. In pressure systems, on the other hand, the product is moved by an increase in atmospheric pressure. We will see that there are also systems with a mixed configuration, i.e. with depressurised and pressurised sections.
There are various factors which influence the design of these systems and which must be taken into consideration, also when deciding whether to opt for a pneumatic conveying system in pressure or in depression. First of all, the characteristics of the material to be moved, such as volume, weight, size, friability, abrasiveness and hygroscopicity and its physical properties, such as density, retention and air permeability. Then come the constraints due to the customer’s requirements and the conformation of his production site: these influence the calculation of kilos per hour, of the length of the horizontal and vertical pipes and their diameter, and of the systems for feeding and discharging the material at the pick-up and delivery points.
Pneumatic pressure conveying systems
The special feature of pneumatic pressure conveying systems is that the fan, i.e. the electrical machine that produces the necessary air and pressure, is positioned upstream of the system. All the pipes and the various components are in excess pressure relating to the atmosphere. Thanks to an injection system, which plugs into the pipe, the material is fed into the pipe, transported and conveyed to its destination. Depending on requirements, the product can be fed through a sealed roller, an injector, a screw conveyor, a double-valve feeder or a propeller. At the arrival points, the product is separated from the air by special filtering devices such as cyclone separators. Pneumatic pressure conveying is usually used to handle relatively heavy materials and when is required transport from one source to several destinations.
ADVANTAGES
- longer distances can be covered than with suction systems
- air density better supports the material
- greater pressure differences are achieved
- the discharge section has a small footprint
- ease of use and assembly
DISADVANTAGES
- difficulty in feeding the material into the circuit
- the considerable overall dimensions at the loading point due to the presence of the product feeding parts
- possibility of air leaks at the loading point
- easy generation of condensation
- in the event of an imperfect seal, the material may leak out
- higher cost of pipes and auxiliary parts due to the high pressures involved
- high pressure pushes the product in a rude manner with the possibility of damaging it
- high energy consumption, bordering on inefficiency for high flow rates
- increased wear and tear on transport lines
- BLOWER
- PRODUCT INSERTION
- TRANSPORT DUCT
- PRODUCT OUTLET
- SEPARATOR
- AIR OUTPUT
- FILTER
Vacuum pneumatic conveying systems
Unlike pneumatic conveying systems under pressure, when we speak about systems under vacuum, because the product is sucked along the pipes, the position of the fan is downstream, to keep the whole system under vacuum. If the material to be transported is of relatively high volume, the first choice for the fan will fall on a side channel blower, or lobe vacuum pumps or rotary vane pumps when higher vacuum levels are required. They are mainly used in chemical-pharmaceutical industry, in food sector and in plastics processing sector for granulate transportation, especially when is required handling without contact with the ambient.
ADVANTAGES
simplicity of construction
the product is moved gently
easy insertion of the material into the system
minimum space required at the feeding point
possibility of sucking material from piles, e.g. directly from trucks
multiple loading points are possible
in the event of an imperfect seal at any point, there is no material spillage.
DISADVANTAGES
limitation of pressure difference and of distances that can be covered
rarefaction of air with consequent less possibility of supporting the material
required space at the outlet due to necessary presence of filters
- BLOWER
- PRODUCT INTAKE
- TRANSPORT DUCT
- PRODUCT OUTPUT
- SEPARATOR
- AIR OUTLET
- FILTER
- AIR HOSE
Mixed pneumatic conveying systems
As can be seen from the diagram in mixed technology systems, there will be one section of the pneumatic conveying system under pressure and one under vacuum. The material moved from the pick-up point to the destination will have to pass through the fan. It follows that this choice is only possible if the material size is very small and if neither the impeller blades nor the material can be damaged.
- BLOWER
- PRODUCT INLET
- DEPRESSURE PIPE
- PRODUCT OUTLET
- SEPARATOR
- AIR OUTPUT
- FILTER
- AIR HOSE
- PRESSURE PIPE
Motions in pipes
The ways the material moves inside the pipes can be chosen according to the specific situation, both for pneumatic transport in pressure and depression. Let’s begin by saying that there are two major modes, which are in antithesis with each other.
In the dilute phase, also known as flight conveying, the material is moved by floating in the air inside the pipes. Isolated material grains are quickly dragged forward, bouncing off walls and colliding with each other. The thrust is given solely by the air action on the material, which must be present in modest quantities to not obstruct too much the air passage and consequently slow down the all movement. This is a pneumatic transport which requires high speed for both gas and material and therefore requires quite a lot of power. The continuous violent impact of the grains risks degrading the material and exerts an abrasive action on the tubes.
On the other hand, in dense phase motion, also known as high pressure, the material inside the pipe does not float, but settles at the bottom of the pipe, filling it partially or completely. This results in low velocities of both gas and material. The advantages are obvious: high flow rates, limited wear and reduced air consumption. On the other hand, there is a greater tendency for the pipes to clog, especially in horizontal sections.
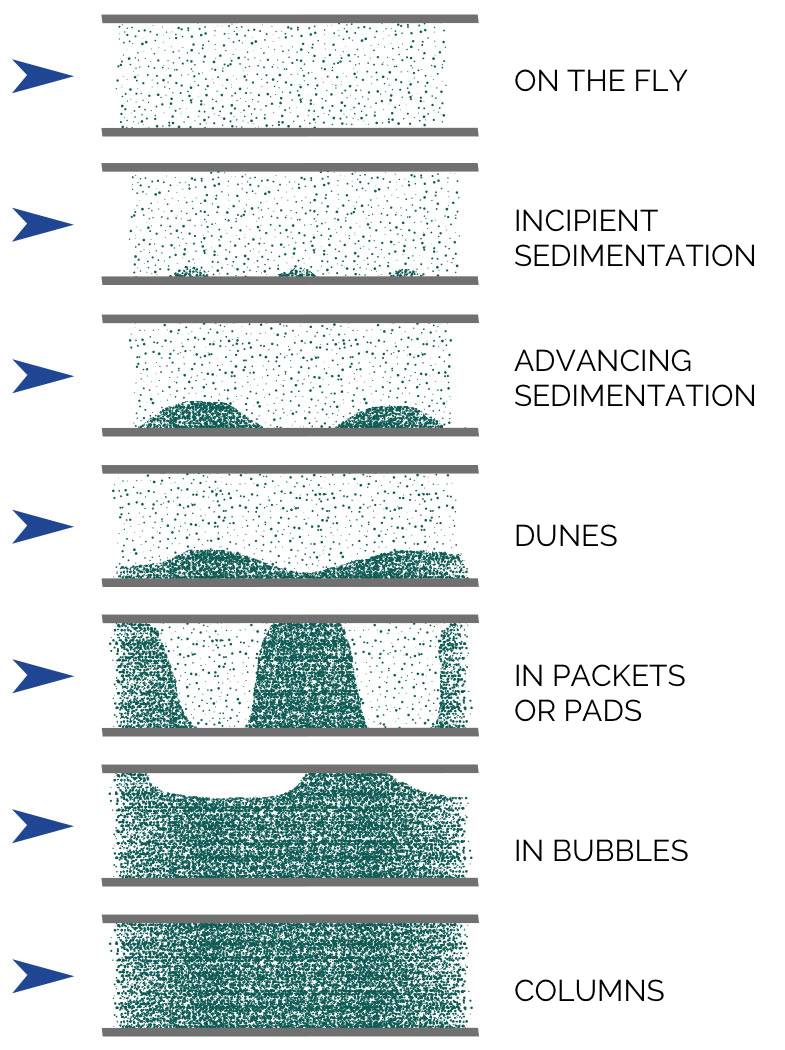
We design, we manufacture, we test
Apply vacuum systems are designed for pneumatic conveying systems under pressure or suction and are tested in every part on the installation site.