We design pneumatic conveying systems
What is pneumatic conveying
Pneumatic conveying is a widely used method in industry for transferring materials from one point to another through closed pipelines. The driving force for the transfer comes from the combination of a pressure difference and the flow of gas within the pipes. The gas is usually air or, depending on requirements, a different gas, such as nitrogen, which being inert is suitable for transporting potentially explosive materials. To fully understand how a pneumatic conveying system works, it is necessary to include other elements in addition to the pipes.
There is equipment to handle the gas, which can be a pump, a blower, a suction unit… equipment to introduce the material into the pipelines and to collect it on arrival, and possibly elements for dedusting. Although the most commonly transferred substances are flour, cement, sand or plastics, also chemicals, animal feed and minerals can be moved pneumatically. These are all materials with a very low moisture content, while substances in paste or liquid form are not suitable for this mode of handling. A pneumatic conveying system can also be designed without the material to be conveyed coming into direct contact with moving parts.
How pneumatic conveying works
To move material, as with any other work, energy is needed. In our case, pneumatic conveying works because energy is provided by the pressure differential (measured in kilograms per square centimetre) and the air flow (measured in cubic metres per second). The air pressure on the line is determined by the device that manages it and generates the pressure or vacuum and its position within the system determines whether one or the other is generated. If it is positioned at the beginning, the air will be pushed into the pipes and therefore works under pressure. If it is positioned at the end of the line, the air will be extracted and therefore works under vacuum.
By properly controlling the pressure or vacuum and the air flow within the system, the material can be transferred. These parameters vary mainly according to what has to be conveyed (flow characteristics, grain size, specific weight), the profile of the conveying line (pressure drop) and the desired performance. This is why a system designed for one material may not be suitable for another.
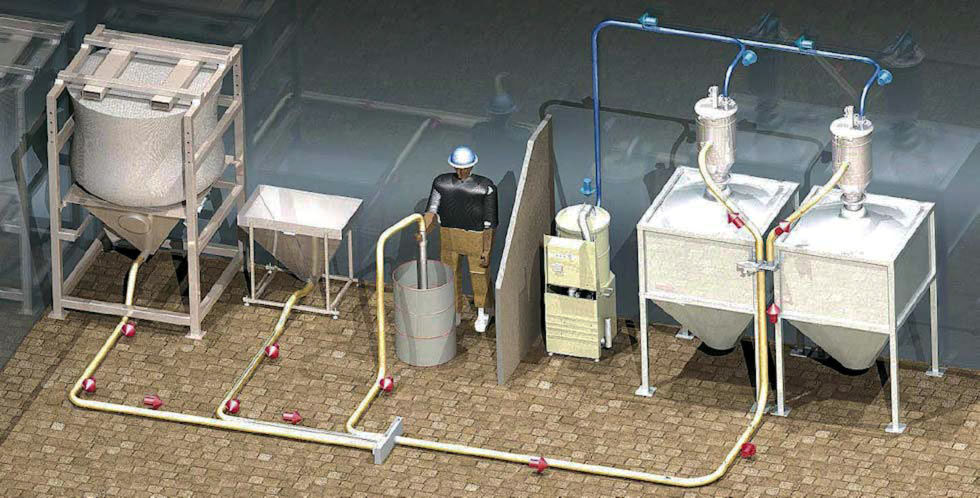
Fields of application
Whether in powder or granular form, a wide variety of materials can be moved and stored in many industrial contexts using pneumatic conveying. Moving materials is essential in areas such as agriculture, mining, chemistry, pharmaceuticals, paint production and metal treatment. Agriculture is a particularly suitable field, dealing with tonnes of materials: think of grain and rice crops, animal feed and fertilisers. Food processing could benefit greatly from the use of pneumatic conveying when processing or packaging flour, tea, coffee and sugar.
The mining and quarrying sector, where more or less fragmented minerals are processed, is another interesting area for pneumatic conveying applications. In energy production plants to move pulverised coal, lump coal and ash, without any dispersion. In the chemical industry where there are so many materials to be moved in so many forms. Sand for foundries and in glass production. Cement and alumina are other materials that are pneumatically handled in huge tonnages in a wide variety of industries.
Conveying modes
The material transferred inside the tubes can be moved continuously, even 24 hours a day, or in batches, i.e. separate quantities of material. For both modes, from an operational point of view, there are two main types of transfer. Understanding these types is essential to gain a clearer idea of how a pneumatic conveying system works.
If the material is transported in suspension in the air, without flowing along the inner wall of the tubes, then we are in presence of what is known as dilute phase transport, also known as liquid or fluid phase transport. If, on the other hand, the material is moved at low speed, not in suspension, through the whole tube or flowing only along a part of it, then we speak of dense phase transport. There is also a third hybrid mode: semi-dense phase transport. In all cases the system can operate, as already specified, in suction or in pressure.
Diluted phase convey
In order to understand how a diluted phase system works, we start by thinking of a road on a windy day. As you walk, you are hit by dust and all kinds of things, picked up by the fast-moving wind. The faster the wind, the more you get hit by objects; the faster the wind, the more it lifts large objects. In borderline cases, a tornado or hurricane can move cars, pieces of houses and large tree branches exactly in the same way as a diluted phase of pneumatic conveying.
Just as wind, a dilute phase pneumatic system relies on air flow speed to pick up small pieces of material and hold them in suspension along the transport line. The chosen speed depends on the size of the material particles and their density. The comparison with a windy day also makes it clear that a dilute phase pneumatic conveying system is capable of handling any type of material, regardless of its density and shape. Although the material is suspended in the air stream, contact with the duct walls is not reduced to zero and increases where the pipes have bends.
The friability and abrasiveness of the material must therefore be carefully considered in the project phase. In a standard diluted phase pneumatic conveying system, at the beginning the air runs at minimum speed, because this first part of the route is considered by the engineers the most critical area. It is here that the material is introduced and must be immediately “captured” by the flow, avoiding clogging.
Air temperature, humidity and the altitude where the system is located must also be taken into account in the dilute phase design.
Diluted phase pneumatic conveying under pressure
This is the most common type for moving powders and granules. Widely used for non-friable materials with low abrasiveness and low specific weight, it is not suitable for mixed products. Typical examples are flours, sugars, plastic granules, sodium bicarbonate and zinc oxide. In the initial part of the system, a low-pressure compressed air generator, such as a lobe or side channel blower, injects a lot of air. The material is then introduced into the pipes via valve or screw pump. It is a simple, economical and ideal system for moving material from a single source to several end points.
Conveying modes
There are essentially two ways of moving material. In flight conveying the concentration of material in the flow is low, so the particles travel floating along the entire path. With proper design it is a flexible mode and suitable for any material of any specific weight. With the fluidising mode at the top of the pipe the material is transported on the fly while at the bottom most of it remains displaced by the flow. It can only be used with very fine, dry materials that allow air to pass between the particles and make them flow.
Diluted phase pneumatic conveying under pressure
This is the most common type for moving powders and granules. Widely used for non-friable materials with low abrasiveness and low specific weight, it is not suitable for mixed products. Typical examples are flours, sugars, plastic granules, sodium bicarbonate and zinc oxide. In the initial part of the system, a low-pressure compressed air generator, such as a lobe or side channel blower, injects a lot of air. The material is then introduced into the pipes via valve or screw pump. It is a simple, economical and ideal system for moving material from a single source to several end points.
Diluted phase pneumatic conveying in depression
Although this type of dilute phase pneumatic conveying is less efficient, it has features that make it suitable for special situations. For example, when there is not much space available for the installation of other types of machines such as rotary valves or thrusters. It is also suitable for extracting material from multiple sources and directing it to a single destination, or when short distances need to be covered at low flow rates. It is an appropriate choice for handling materials that tend to compact and compress under pressure (such as wood chips and fibrous materials) and for toxic substances that must not be released into the environment.
Semi-dense phase conveying
This is the least common type of pneumatic conveying. The air velocity is between that used in dilute phase and dense phase systems. The lighter product particles are transported as in dilute phase conveying, while the heavier particles are transported in “blocks”.
The system is configured in the same way as the dense phase systems, but uses pressure vessels with fluidising bottoms. It can thus handle semi-abrasive powders and powders that require prior aeration to be discharged into the conveying line. Typical examples are cement and fly ash.
A trusted partner
Apply has always designed pneumatic conveying systems according to your needs, offering the best solution at the best price.